1.0 OBJECTIVE
To lay down a procedure for Change Control.
2.0 SCOPE
The SOP is applicable to any change in the documentation and facility required to be carried out to make amendments, rectify errors, improvements, meet regulatory/ statutory/ legal requirements. It shall be applicable to all Departments at XYZ pharm.
3.0 RESPONSIBILITY
- Initiator – Concerned Department
- Head – Concerned Department
- Head – Quality Assurance
4.0 DEFINITION(S)
Change Control is define as A formal system by which qualified representatives of appropriate disciplines review proposed or actual changes that that might affect a validated status. The intent to determine the need for action that would ensure that the system is maintained in a validated state.
5.0 PROCEDURE
5.1 A Change Control Form (Annexure – II & III) shall be initiated for the following changes but not limited to:
- Document related
- Standard Test Procedures/Specifications/GTP’s.
- Batch Manufacturing Records/Batch Packing Records/MMF
- Formats
- Validation
- Vendors
- New product manufacturing
- Others
- B Facility Related
- Facility
- Equipment/Instruments
- Others
5.2 Classification scheme:
- 5.2.1 Present status and proposed changes shall be filled and forward to the HOD for justification and evaluation.
- 5.2.2 The HOD shall also attach appropriate data or back-up document(s), drawing(s), in support of the change proposal.
- 5.2.3 If the proposed change calls for changes related to documents, the proposed draft of document shall be attached.
- 5.2.4 Similarly, if the proposed change calls for changes related to Facility, a proposed Facility change draft document shall be attached.
- 5.2.5 Upon justification, Change Control Form shall be forwarded to QA for evaluation.
- 5.2.6 The proposed changes shall be evaluated by QA Head or his designee to determine to which category they belong.
- 5.2.7 QA Head or his designee shall determine the category of proposed change as ‘Minor, Moderate or Major, depending on the nature and degree of changes, and the effect the change could impart.
- 5.2.8 QA Head or his designee may, if necessary, consult the Regulatory Affairs for appropriate classification of the change, from Regulatory perspective.
- 5.2.9 QA Head or his designee evaluates the requirement of review of other Department based on the nature of change proposed.
- 5.2.10 Few examples of each category of change are provided in the Annexure–IV.
- 5.2.11 Minor Change: A Minor change is described as a change which,
- a. is unlikely to have an impact on the quality or process attributes of the product.
- b. does not impact the process, significantly.
- c. is reviewed and approved by QA Head
- d. may require minimal testing and revalidation.
- e. has no impact on regulatory filings.
- 5.2.12 Moderate Change: A Moderate change is described as a change which,
- a. is usually for improvements to process, product, procedure, materials, equipment or system;
- b. is a change which may not have an adverse effect on the quality of the product, however proper evaluation is necessary ;
- c. is evaluated and approved by QA Head
- d. may not affect the regulatory status of the product/process.
- 5.2.13 Major Change: A Major change is described as a change which,
- a. is likely to have an impact on the critical attributes of the process, procedure or product.
- b. could shift the process significantly, affecting the quality, yield, stability, impurity profile.
- c. warrants definite additional/major testing and suitable Revalidation studies to justify the change.
- d. is evaluated and approved by QA Head.
- QA Head shall consult Head–Regulatory Affair for changes that may affect the regulatory filings of the Product/process.
5.3 Change Control Approval
- 5.3.1 QA Head or his designee shall log the details of change control in the Change Control Register as per Annexure-I.
- 5.3.2 The Regulatory Affairs shall determine whether the proposed change infringes any related documentation already submitted to agencies.
- 5.3.3 The Regulatory Affairs shall then return the Change Control Form to QA Head for approval.
- 5.3.4 QA Head or his designee shall evaluate the Change control form ( but not limited to)
- impact on quality of product vis-à-vis in-house specifications and specific customer requirements
- impact on regulatory commitments
- impact on process performance, or yield
- impact on stability, impurity profile
- impact on performance of STP
- impact on test limit
- need to inform customers, Regulatory agencies
- similarity of the process/equipment condition after the change is implemented
- impact on related documents
- maintenance and changes of equipment instrument(s)
- 5.3.5 QA Head shall be responsible to,
- provide inputs on type of validation to be carried out
- review and approval of applicable protocol
- verify and confirm the validation report
- check compliance to the protocol
- 5.3.6 If QA Head determines the Change Control Form as acceptable and does not require confirmation of the proposed change, prior to implementation, he shall approve it with signature and date.
- QA Head or his designee shall assign a distinct Control number to the approved Change Control Form, for traceability, as per following pattern:
- CCD/24/01: For document related changes
- CCF/2101: For Facility related changes
- Where,
- CCD or CCF stands for Change control for document or Change Control for Facility related
- / Stands for slash
- 24 stands for year 2024
- 01 stands for serial no.
- 5.3.8 QA Head shall return the copy of the rejected Change Control Form to Concerned HOD with comments, if it is found unacceptable.
- 5.3.9 In case of changes in documents, the revised documents shall be printed and issued to the concerned Departments as per standard operating procedure.
- 5.3.10 In case of changes in the process, revised process documents shall be printed and issued to the concern Departments as per standard operating procedure.
5.4 Changes required for Confirmation, prior to implementation
- 5.4.1 In case the QA Head finds it necessary to confirm the proposed change, prior to implementation, he shall refer to the initiating Department head.
- 5.4.2 In such case, the deviation shall be raised as per Deviation handling SOP (QAD/028) for confirming the activity, and a time frame shall be recommended for the completion of the activity.
- 5.4.3 A protocol for activity, duly approved by QA Head, shall be put in place.
- 5.4.4 The HOD, in coordination with QA Head shall perform the activity as per the approved protocol. Where required, the HOD shall seek the help of Engineering Department.
- 5.4.5 The report shall be prepared, reviewed and approved as per protocol.
- 5.4.6 If the report is found acceptable, QA Head shall approve the Change Control Form with signature and date.
- 5.4.7 This shall be further approved by Head – Corporate QA
5.5 Distribution of Approved Change Control Form Copies
- 5.5.1 The original signed and approved Change Control Form along with the back-up documents shall be retained with Quality Assurance.
5.6 Communication to users and Customers
- 5.6.1 The HOD, who had initiated the Change Control Form, shall be responsible to communicate the approved and implemented changes to the affected users of the Department.
- 5.6.2 Regulatory Affairs shall communicate for updates to regulatory agencies, where required.
- 5.6.3 QA Head shall also communicate the changes to QA personnel, who are concerned with changes.
5.7 Closure
- 5.7.1 The HOD of the concerned Department and the QA Head shall ensure that the affected documents and activities are completed and closed.
- 5.7.2 QA Head shall review whether the changes are implemented and all necessary to following actions to be completed:
- Validation/Qualification activity & report,
- BMR/BPR.
- Specification, GTP’s and STP’s Master files updation (after signature).
- Drawings, or their updation.
- Communication to users & customers.
- Communication to RA.
5.8 Preservation of Records
- 5.8.1 All original Change Control Forms shall be filed with QA Department.
6.0 ABBREVIATION(S)
- HOD : Head Of Department
- QA : Quality Assurance
- RA : Regulatory Affairs
7.0 REFERENCE(S)
- NA
8.0 ANNEXURE(S)
- ANNEXURE – I : Change Control Register
- ANNEXURE – II : Change Control Form (Document related)
- ANNEXURE – III : Change Control Form (Facility related)
- ANNEXURE – IV : Example of Major, Moderate & Minor Changes
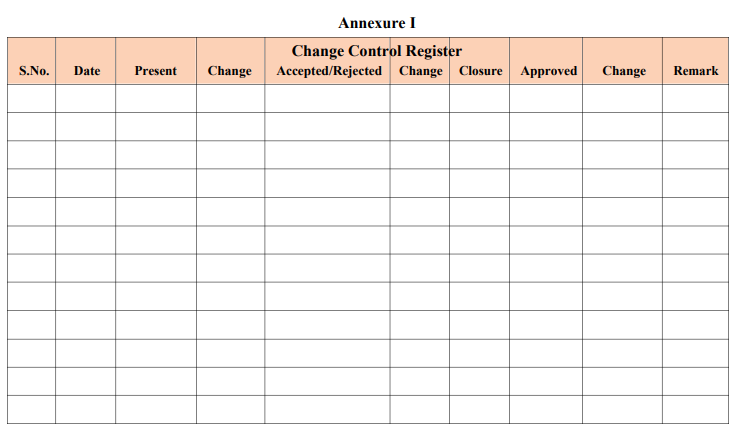
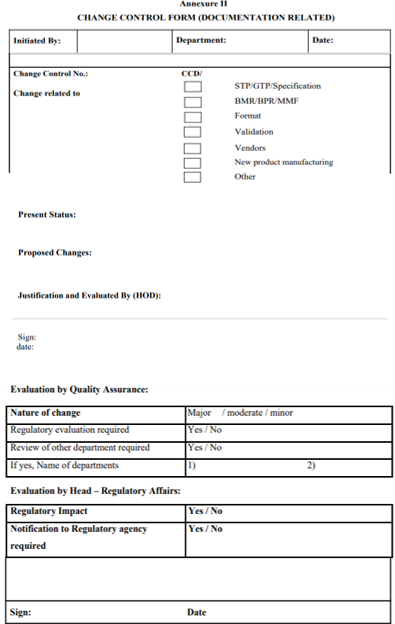
Annexure IV
EXAMPLE OF MAJOR, MODERATE AND MINOR CHANGE
1. Major change:
Manufacturing Site
- Changing to a site, which has never been inspected for the type of operation to be performed.
- Change in manufacturing site for all processes except the main process.
Manufacturing Process
- Fundamental changes in manufacturing process or technology.
- Change in process of manufacturing affecting the impurity profile and / or the physical, chemical, or biological properties.
- Establishing new processing methods.
- Changes related to the starting material at all stages.
- Change in key materials or its source.
- Change in packaging mode.
Manufacturing Equipment
- Change in equipment, which is significantly different from the previous one even when there are no modifications to the process parameters.
- Change in different kind of equipment e.g. Blister Packing
Shelf Life
- Extension of expiration dating period based on new/revised stability protocol or on full time shelf life data.
Specifications/STP’s
- Relaxing the acceptance criteria.
- Deleting any part of specification.
- Change in STP used for testing : Packaging components, final drug products or raw materials.
- Revision in specification limits of critical parameter (such as Assay, Related substance, Residual solvent impurities etc.)
2. Moderate change:
Manufacturing Site
- Change in manufacturing area for final drug product (to different location, different area within the building).
Manufacturing Process
- Change in process / or process parameters.
- Improvement in process capability, efficiency.
- Change in Batch size
- Revision of BMR and BPR after Validation
Specifications
- Adding a new test and associated STP and acceptance criterion to a specification, that provides the same increased assurance as the STP described in approved application.
3. Minor change:
Manufacturing Equipment
- Like to like equipment changes.
Manufacturing Process
- Change in dimensions of secondary or tertiary packing materials
- Change in item codes
Read also: SOP for CAPA (Corrective and Preventive Action) Handling Procedure